Imagine living in a world where your home cleaning system is as advanced and seamless as the technology in your smartphone. That’s the promise of a central vacuum system, a game-changer in home maintenance. However, the thought of installing such a system can be daunting, especially when it comes to the wiring aspect. Surprisingly, a study suggests that a significant number of homeowners shy away from DIY home improvement projects due to a lack of clear, step-by-step guidance.
This blog post aims to demystify the process of connecting central vacuum wiring, offering a straightforward solution to what may seem like a complex task.
Materials Needed for Connecting Central Vacuum Wiring
Embarking on the journey of installing a central vacuum system in your home? Here’s a comprehensive list of the materials you’ll need to ensure a smooth and successful installation. Remember, having the right tools and materials at hand not only makes the process more efficient but also ensures a safer installation.
- Central Vacuum Unit: The heart of the system, this unit is responsible for creating suction and collecting debris.
- Wiring: Typically, 14-2 or 12-2 gauge wiring is recommended. Ensure it’s suitable for residential electrical systems.
- Low Voltage Wire: This is used to connect the vacuum inlets to the central unit, enabling the system to turn on automatically when the hose is plugged in.
- Electrical Tape: Essential for insulating and securing wire connections.
- Wire Nuts: These are used to safely connect and cap off wire ends.
- Vacuum Tubing: This is the piping that transports dirt and debris from the vacuum inlets to the central unit. PVC piping is commonly used.
- Vacuum Inlet Valves: Installed in various locations around your home, these are the points where you plug in the vacuum hose.
- Power Drill: Necessary for drilling holes for the tubing and inlet valves.
- Fish Tapes: Useful for pulling wires through walls, ceilings, and vacuum tubing.
With these materials in hand, you’re well on your way to installing a central vacuum system that will bring a new level of cleanliness and convenience to your home.
Household Circuit Requirements
When installing a central vacuum system, it’s crucial to ensure that your household’s electrical circuit can safely and efficiently handle the system’s power requirements. Here’s a breakdown of the dedicated circuit requirements and code considerations for the location and accessibility of connections:
Dedicated Circuit Requirements
- Voltage: Most central vacuum systems are designed to operate on a standard 110-120 volt household circuit.
- Breaker Size: The breaker size depends on the specific model of the central vacuum unit. Typically, a 15-20 amp breaker is sufficient, but always refer to the manufacturer’s specifications.
- Circuit Type: It’s advisable to have a dedicated circuit for the central vacuum system to prevent overloading. This means the system should be the only appliance on that circuit.
Code Requirements for Location/Accessibility
- Accessibility: The central vacuum power unit should be installed in an easily accessible area for maintenance and emptying the debris collection. Common locations include the garage, basement, or utility room.
- Safety Codes: Installation must comply with local building and electrical codes. This often includes requirements for the type of wiring, conduit, and proper grounding.
- Distance from Inlets: The power unit should be strategically placed to ensure optimal performance. It should be located centrally to minimize the distance to each vacuum inlet valve, reducing the risk of clogs and maintaining strong suction.
- Ventilation: If the system requires venting, ensure it’s done according to local codes, typically venting to the outside of the home to expel exhaust air.
In-Wall Tubing Installation for Central Vacuum Systems
Installing the in-wall tubing for a central vacuum system is a critical step in ensuring efficient and effective operation. Here’s a guide to help you through the process, from selecting the right tubing to properly installing it within your home’s walls and floors.
Recommended Tubing Size/Material
- Size: The standard size for central vacuum tubing is 2 inches in diameter. This size is optimal for maintaining strong suction and preventing clogs.
- Material: High-quality PVC tubing is commonly used due to its durability, ease of installation, and resistance to wear.
Mapping Out Tubing Layout
- Plan the Route: Before cutting or drilling, map out the most direct path from each inlet valve to the central unit. Avoid sharp bends or long horizontal runs to maintain efficient airflow.
- Inlet Placement: Inlets should be strategically placed for easy access in every part of the house. One inlet typically covers about 600-700 square feet.
Fishing Tubing Through Walls and Floors
- Use Fish Tape: To route tubing through walls and floors, use fish tape or a similar tool to pull the tubing through the designated path.
- Consider Obstacles: Be aware of electrical wiring, plumbing, and structural elements when planning the tubing route.
Cutting Tubing to Size
- Measure Twice, Cut Once: Accurately measure the required length of tubing before cutting.
- Clean Cuts: Use a tubing cutter or a fine-toothed saw to make clean, straight cuts. This ensures a better fit and easier installation of the tubing sections.
Joining Tubing Sections Properly
- Use PVC Cement: Apply PVC cement to the outside of the pipe end and inside of the fitting. Join them quickly and hold for a few seconds to ensure a secure bond.
- Maintain Alignment: Ensure that the tubing sections are properly aligned to avoid any airflow restrictions.
- Secure Connections: Use PVC couplings to join straight sections of tubing. Elbows and T-fittings are used for changing directions or adding branches to the system.
How to Connect Low Voltage Wires to Central Vacuum
Low voltage wiring is a crucial component of a central vacuum system, as it connects the inlet valves to the central unit, enabling the system to turn on when the hose is plugged in. Here’s a guide on wire sizing per circuit length and a comparison of different wire types, along with information on where to connect them.
Wire Sizing Guide per Circuit Length
Circuit Length (Feet) | Recommended Wire Size (AWG) |
---|---|
0 – 50 | 20 |
51 – 100 | 18 |
101 – 150 | 16 |
151 – 200 | 14 |
Over 200 | Consult a professional |
Types of Low Voltage Wires
Type | Description |
---|---|
Single Conductor | Used in some older systems; requires running two separate wires for each connection. |
Jacketed 2-Wire | Most common; consists of two insulated wires enclosed in an outer jacket, simplifying installation. |
3-Wire | Includes an extra wire, often used for systems with additional features or controls. |
Connection Points
Terminals on Unit: Most central vacuum units have low voltage terminals where the wires from the inlet valves are connected. These terminals are typically clearly marked and located in an easily accessible area on the unit.
Low Voltage Junction Box: In some installations, especially those with multiple inlet valves, a low voltage junction box may be used. This box acts as a central point where all the low voltage wires from the inlet valves converge and are then connected to the central unit.
Note: Always ensure that the low voltage wiring does not run parallel to high voltage wiring for extended distances to avoid potential interference. Also, be sure to follow local electrical codes and standards for low voltage wiring.
Connecting Vacuum Unit to Power Supply
When connecting your central vacuum unit to the power supply, safety is paramount. Always start by shutting off the main breaker panel to eliminate the risk of electrical shock. Here’s a step-by-step guide to help you wire your vacuum unit safely and effectively, along with instructions for testing the connections.
Safety First: Shut Off Main Breaker Panel
- Locate Your Main Breaker Panel: This is usually found in a basement, garage, or utility area.
- Turn Off the Main Power: Look for the main circuit breaker and switch it to the ‘off’ position. This action will cut power to your entire house, so ensure that you have adequate lighting and safety equipment.
Step-by-Step Wiring Instructions
- Prepare the Vacuum Unit: Locate the electrical connection panel on your central vacuum unit.
- Remove the Cover: Unscrew and remove the cover to expose the wiring terminals.
- Strip the Wires: If not already done, strip the ends of the wires from your power source to expose the bare wire.
- Connect the Wires: Attach the live (usually black or red), neutral (usually white), and ground (usually green or bare) wires to their respective terminals on the vacuum unit. Ensure the connections are tight and secure.
- Secure the Connections: Use wire nuts where necessary to secure the connections. Ensure that no bare wire is exposed.
- Replace the Cover: Once all connections are made, replace the cover on the electrical connection panel.
Testing Connections Before Turn On
- Double-Check Connections: Before turning the power back on, double-check all connections to ensure they are secure and correctly matched.
- Use a Multimeter: If available, use a multimeter to test the continuity of the wiring. This step ensures that there are no short circuits.
- Turn Power Back On: Once you are confident in your wiring, return to the main breaker panel and turn the power back on.
- Test the Vacuum Unit: Turn on the vacuum unit to test its operation. Listen for any unusual sounds and ensure that the unit powers up correctly.
- Inspect During Operation: Briefly inspect the unit while it’s operating to ensure there are no sparks, smoke, or unusual smells, which could indicate a wiring problem.
Safety Tip: If you are not comfortable or familiar with household wiring, it is highly recommended to consult or hire a licensed electrician to perform this task. Electrical work can be dangerous and should be handled with care and knowledge.
Inlet Valve and Tubing Connections
Properly installing inlet valves and connecting them to the tubing is crucial for the efficient operation of your central vacuum system. Here’s a guide on how to mount inlet valves in strategic locations, cut tubing to size, connect tubes securely to valves, and check airflow.
Mounting Inlet Valves in Strategic Locations
- Plan Placement: Inlet valves should be evenly distributed throughout the home. Typically, one inlet can cover about 600-700 square feet. Place them in locations that allow easy access to all areas with the vacuum hose.
- Choose Wall Locations: Inlet valves are usually mounted on interior walls. Avoid placing them behind doors or in areas where furniture might block access.
- Mark and Drill: Once you’ve determined the locations, mark the spots for drilling. Use a stud finder to avoid drilling into studs, and ensure there are no electrical wires or plumbing in the drilling area.
Cutting Tubing to Size
- Measure Accurately: Measure the distance from the vacuum unit to each inlet valve location.
- Make Clean Cuts: Use a tubing cutter or a fine-toothed saw to cut the tubing. Ensure the cuts are straight and clean for a better fit.
Connecting Tubes Securely to Valves
- Dry Fit First: Before gluing, dry fit the tubes to the inlet valves to ensure a proper fit.
- Apply PVC Cement: For PVC tubing, apply PVC cement to both the tube and the valve connection. Push them together and hold for a few seconds to ensure a strong bond.
- Secure the Connection: Make sure the connection is tight and secure. Use clamps if necessary to hold the tubing in place while the cement sets.
Checking Airflow at Valves
- Test Each Valve: After installation, turn on the vacuum system and test each inlet valve by opening it and checking for strong, consistent airflow.
- Listen for Air Leaks: Listen for any hissing sounds that might indicate air leaks. If you find a leak, recheck the connections at that valve.
- Use a Vacuum Gauge: If available, use a vacuum gauge to measure the suction at each inlet. This can help ensure that the system is balanced and working efficiently.
Testing System Operation
After installing your central vacuum system, it’s essential to test its operation to ensure everything is working correctly. Here’s a step-by-step guide on how to power up the vacuum unit, check wiring connections, assess airflow at inlet valves, adjust any loose connections, and provide troubleshooting advice.
Powering Up Vacuum Unit
- Ensure Safety: Before powering up, make sure all connections are secure and the area is clear of tools and debris.
- Turn On the Power: Switch on the power at the main breaker and then at the vacuum unit. Listen for the sound of the motor to ensure it starts smoothly.
- Observe Initial Operation: Check for any unusual noises or smells that could indicate a problem. The unit should run smoothly without any hitches.
Checking Wiring Connections
- Inspect Low Voltage Wiring: Ensure that the low voltage wiring from the inlet valves to the vacuum unit is properly connected and secure.
- Test Inlet Activation: Plug a hose into each inlet valve to check if the system activates correctly. The vacuum should start automatically when the hose is inserted.
Assessing Airflow at Inlet Valves
- Check for Consistent Suction: Test each inlet valve for suction. The airflow should be strong and consistent at each point.
- Listen for Air Leaks: While the system is running, listen for any hissing sounds that might indicate air leaks in the tubing or at the connections.
Adjusting Any Loose Connections
- Tighten Connections: If you find any loose tubing connections or inlet valves, tighten them. Use appropriate tools to ensure the connections are secure.
- Reapply Cement if Necessary: For PVC tubing connections that are loose, you may need to reapply PVC cement for a more secure bond.
Troubleshooting Advice
- No Power or Suction: If the unit doesn’t turn on, check the power supply, fuses, and circuit breakers. Ensure the unit is properly plugged in and the switch is on.
- Weak Suction: If suction is weak at an inlet, check for blockages in the tubing, kinks, or leaks. Also, check if the collection container is full or if the filter needs cleaning.
- Unusual Noises: Rattling or banging sounds can indicate a blockage or a problem with the motor. Turn off the system and inspect for obstructions or damage.
- Professional Help: If you encounter complex issues or are unsure about any aspect of the system’s operation, don’t hesitate to contact a professional for assistance.
Safety Precautions for Installing and Operating
When installing and operating a central vacuum system, safety should always be your top priority. Here’s a list of key safety precautions to prevent electric shock, ensure proper ventilation, and adhere to building codes.
Preventing Electric Shock
- Turn Off Power: Always turn off the main power at the breaker panel before starting any installation or maintenance work.
- Use Insulated Tools: When working with electrical components, use insulated tools to reduce the risk of electric shock.
- Check for Live Wires: Use a voltage tester to ensure no live wires are present in the area where you are working.
- Proper Wiring and Grounding: Ensure all electrical connections are properly wired and grounded according to the manufacturer’s instructions and local electrical codes.
- Avoid Water Exposure: Keep all electrical components dry and avoid installing electrical parts in areas prone to moisture.
Allowing Proper Ventilation
- Ventilation for Motor: Ensure the central vacuum unit is installed in a well-ventilated area to prevent overheating.
- Exhaust Venting: If your system requires external venting, make sure it is properly installed to expel exhaust air outside the home.
- Clearance Around Unit: Maintain adequate clearance around the vacuum unit to ensure unrestricted airflow.
Following Building Codes
- Adhere to Local Codes: Familiarize yourself with and adhere to local building and electrical codes during installation.
- Professional Inspection: Consider having your installation inspected by a professional to ensure it meets all safety standards and codes.
- Use Approved Materials: Only use materials and components that are approved for use in central vacuum systems and meet safety standards.
- Regular Maintenance: Regularly inspect and maintain your system to ensure it continues to operate safely.
Final Thought
As we wrap up our journey through the intricacies of connecting central vacuum wiring, it’s worth pondering the broader implications of such a task. This isn’t just about wiring or home improvement; it’s a testament to the evolving relationship between humans and their living spaces. The seamless integration of a central vacuum system symbolizes our continuous quest for efficiency, cleanliness, and convenience in our homes. It reflects a deeper desire to harmonize our living environments with technology, making our daily routines more effortless and sustainable.
In the grand tapestry of home innovation, the act of connecting central vacuum wiring is more than a technical endeavor; it’s a small, yet significant stitch in the fabric of modern living. It challenges us to think about how every improvement, no matter how small, contributes to a larger narrative of progress and comfort. As you embark on this task, remember that you’re not just installing a system, but you’re also weaving your own thread into the ever-evolving story of home innovation.
Wiring a Central Vacuum System (FAQs)
What size wire do I need for central vacuum?
For a central vacuum system, the wire size typically depends on the distance and the system’s electrical requirements. Generally, 14-2 or 12-2 gauge wire is suitable for most installations. It’s important to refer to the specific requirements of your vacuum system and adhere to local electrical codes.
How do I run a wire from one outlet to another?
To run a wire from one outlet to another, first, turn off the power to the circuit. Then, install a new outlet box at the new location. Run the appropriate gauge wire from the existing outlet to the new one, through the walls or along the baseboards, using a fish tape or similar tool. Finally, connect the wires to the new outlet, ensuring they are securely attached and the outlet is properly grounded. Always follow local electrical codes and safety guidelines.
Can I install a central vacuum system in an existing home without damaging the drywall?
Yes, you can install a central vacuum system in an existing home with minimal damage to the drywall. Strategic planning of the tubing route and careful cutting for inlet valves can preserve the integrity of the drywall.
What tools are needed to install a central vacuum system in a new construction?
For new construction, you’ll need a hammer, masonry bit, duct tape, and a flashlight. These tools help in drilling, securing cables, and navigating dark spaces like the attic during installation.
How do I secure the wiring in my central vacuum system?
Use cable ties and duct tape to secure the wiring along the trunk line, especially in areas like the attic or basement. This ensures the wiring is neat and reduces the risk of damage.
What accessories are essential for a complete central vacuum system?
Essential accessories for a central vacuum system include a canister, power brush, and various cleaning attachments. These enhance the system’s functionality, especially in areas like the laundry room.
How do I prevent condensation in the tubing of my central vacuum system?
To prevent condensation in the tubing, ensure proper insulation around the pipes, especially if they run through unheated spaces like the attic. Also, check that the system’s vent is correctly installed to regulate air flow.
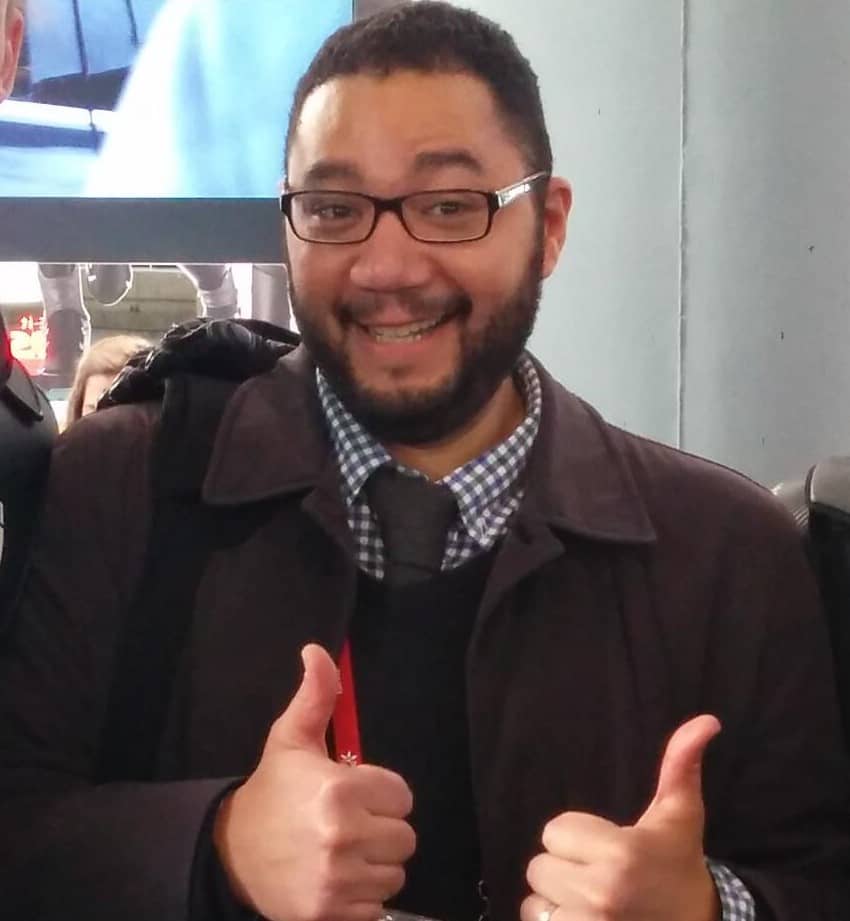
Brian Bennett is an experienced central vacuum expert who has written extensively on the topic. His articles cover a variety of topics related to central vacuum systems, including installation, maintenance, and troubleshooting. Brian also offers a variety of helpful tips and tricks for optimizing central vacuum performance.